In board printing, inks have excellent properties in paper and board printing due to their good performances in abrasion resistance, printability, coating thickness, dot gain, etc., and low content of VOCs (1). Well represented. The following focuses on some of the important factors in ink printing. Ink transfer is often defined as the ability of the substrate to absorb ink. However, this is not very appropriate because it means that the printing paper absorbs a large amount of ink, which may cause excessive consumption of the ink. The use of "ink ink" to express it is more widely accepted and used, this expression may be more accurate. The permeation of the ink is affected by factors such as pressure, the type of ink used, the surface smoothness of the paper, and the size of the pores. The absorption of ink by a paper sheet is often effected by a capillary tube. Some acidic papers can speed up the drying of ink by neutralizing the soluble amines in the ink. The principle of ink drying is that the paper absorbs a sufficient amount of liquid components in the ink through osmosis so that the pigment is captured by the resin and fixed on the surface of the paper. The best result is that only the ink that meets the ink density and quality requirements is transferred in the minimum amount and is firmly adhered to the paper surface. Smooth-surfaced papers (such as double coated paperboard and single-coated paperboard) are printed with less ink, while rough-surfaced paper (with lower hiding power) is consumed due to the need to fill the surface with tiny pits. More ink. If you exclude the choice of media type and ink adjustment two factors, the surface roughness of the paper will also produce a higher dot gain value. The extent of dot expansion depends on the type of paper, the surface structure of the paper, and the size of the air holes. The ink was applied to the paper. If the ink spreads over the paper surface, it is evident that the dot expansion is significant. It is very important that the ink stays on the surface of the paper and there is no excessive separation between the binder and the colorant. Otherwise, poor wear resistance and chalking of the ink will result. An important aspect of printability is overprinting, where different colors overlap by a given design. Overprinting refers to a layer of ink superimposed on another layer of ink, requiring the first layer of ink to be dry enough before the second layer of ink is overlaid. This requirement is more important for double-sided coated paper and single-sided coated paper than for non-coated paper. It is much easier to obtain a satisfactory overprint on the loose side of uncoated paper. If the coated paper cannot be dried to the best condition after printing, we may consider changing the order of the printing processes. The influence of temperature on the control of the drying temperature is crucial because the flow properties of the ink depend mainly on the temperature. We must be very careful to keep the temperature stable. An increase in temperature causes a decrease in viscosity. For example, as long as the temperature is increased by a few degrees, the syrup will obtain near-water-like fluidity from the immobile liquid material. In the printing process, in particular, a squeegee device is installed and a stable ink transfer amount is required in the printing process, after the ink is properly warmed, its performance will be significantly better than that before warming. This point of view has been widely recognized in those regions where the temperature control of print shops in North America and Northern Europe is alternately affected by the large fluctuations in seasonal temperatures. In order to maintain a stable viscosity, it is necessary to control the amount of diluent. The higher the temperature, the less diluent is needed. The thinner of the ink can largely affect the print thickness of the printed product in the actual site. For inks, the diluent can be water or a diluting solvent. Drying characteristics and viscosity control Ink printing is performed on an absorptive surface to obtain sufficient drying factors including evaporation, infiltration, precipitation, and chemical reaction. Evaporative drying is achieved through the action of air and heat. Hot air blows off the volatile substances in the ink when it passes over the surface of the print. Permeation drying is mainly through the action of capillaries, so that the ink is absorbed by the paper surface. Once the ink is absorbed, the print is no longer easily soiled or transferred to the surface of other objects. Precipitation and chemical reactions also contribute to the drying of the ink. Precipitation is the process by which liquid ink is divided into two forms, solid and liquid. The liquid component is absorbed by the paper fibers and the filtered resin and color paste crosslink on the surface of the paper. Chemicals also contribute to the drying of the ink film, but this does not occur in ink-printing of paperboard because the chemical reactions include oxidation, catalysis of the cross-linking reaction, and accelerated drying by action of ultraviolet, infrared, electron beam, or microwaves. Morphological changes. The ink is easily dried by evaporation during printing. In order to slow down the evaporation speed of ink on the ink fountain roller and the squeegee device, most modern corrugated paper printers are equipped with a closed inking device. For printing, a necessary characteristic of the ink is that it should maintain good fluidity before it is transferred to the surface of the substrate. In-process inks usually require the addition of a suitable amount of thinner to dilute the desired viscosity for printing. The vast majority of printer ink tanks are located below the horizontal line of the printing section. The ink is pumped into the ink tank by an ink pump, and the ink tank is provided with an overflow pipe at a relative position with the ink fountain roller so as to maintain a certain amount of ink in the tank. In the process of continuous circulation, the ink is brought into contact with air in the tank and on the drum, which causes some of the solvent to evaporate, which leads to an increase in viscosity, which in turn leads to an increase in the ink density. Therefore, the amount of water added to the ink not only affects the viscosity, but also affects the ink concentration of the printed product.
Silicone Pet Toothbrush
The silicone pet toothbrush in many ways a wonder material. Its softness and flexibility enable a comfortable fit for humans, while gentle for dogs and cats. It's also an inert, chemically stable substance that is indigestible, making it non-toxic
YDS Product categories of Silicone Pet Supplies, we are specialized manufacturers from China, Silicone Pet Toothbrush, Silicone Pet Collar,Silicone Pet Tags,Silicone Pet Milk Can... wholesale high-quality products of Silicone Pet Toys!
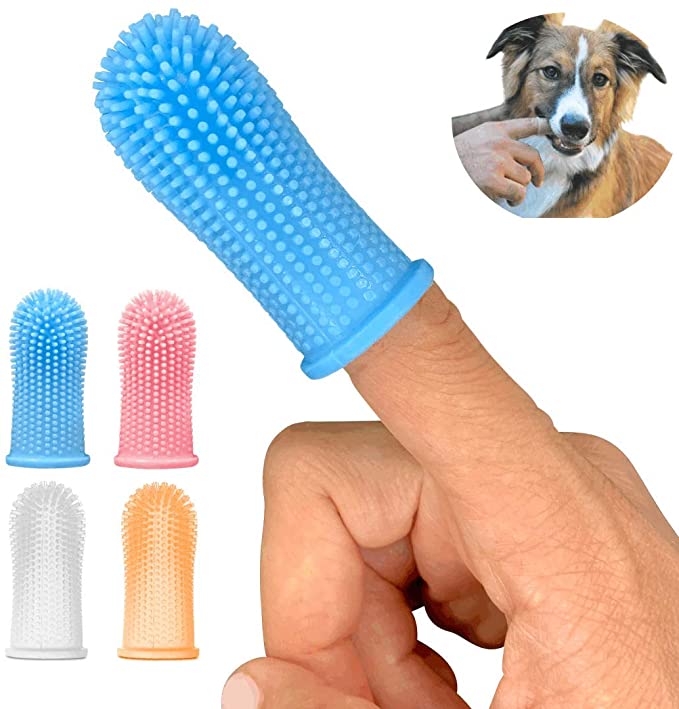
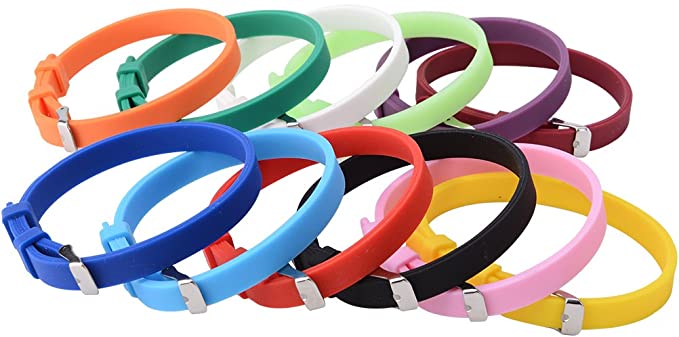
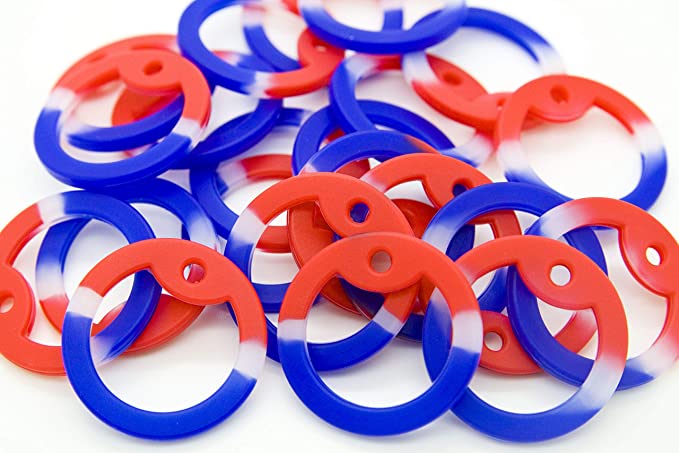
Our Factory Advantages:
1.Mold workshop and 2D and 3D engineer department
2.Solid siliccone compression machine and liquid silicone injection machine
3.Disney and Sedex 4P audit factory
4.ISO 9001,IATF16949,Raw material of FDA LFGB MSDS Certificates
Look forward to your cooperation!
1.Mold workshop and 2D and 3D engineer department
2.Solid siliccone compression machine and liquid silicone injection machine
3.Disney and Sedex 4P audit factory
4.ISO 9001,IATF16949,Raw material of FDA LFGB MSDS Certificates
Look forward to your cooperation!
Cat Dog Finger Toothbrush,Soft Bristle Silicone Pets Finger Brush,Soft High Grade Finger Toothbrush,Pets Dog Finger Toothbrush
Shenzhen Yindingsheng Technology Co., Ltd , https://www.oemsiliconeyds.com